Many engines have gone away from port injection to direct injection. Injecting fuel directly into the combustion chamber, while more fuel efficient, has created an undesirable side effect. Port injection sprays fuel above the intake valves on its way into the combustion chamber. The fuel spray on the intake valves does an excellent job of cleaning the intake valves. Since this no longer happens with direct injection, intake valves are loading up with carbon deposits. Cleaning carbon from intake valves can now be seen as a new maintenance item. Typically recommended at approximately 60k-70k mile intervals. This engine had around 170,000 miles and had not received an intake valve cleaning in the past. There is a lot of buildup on the stems of the valves and all over the intake ports and valves in general. Although hard to notice in the images, one of the port walls had such thick carbon buildup that it was nearing the valve itself.
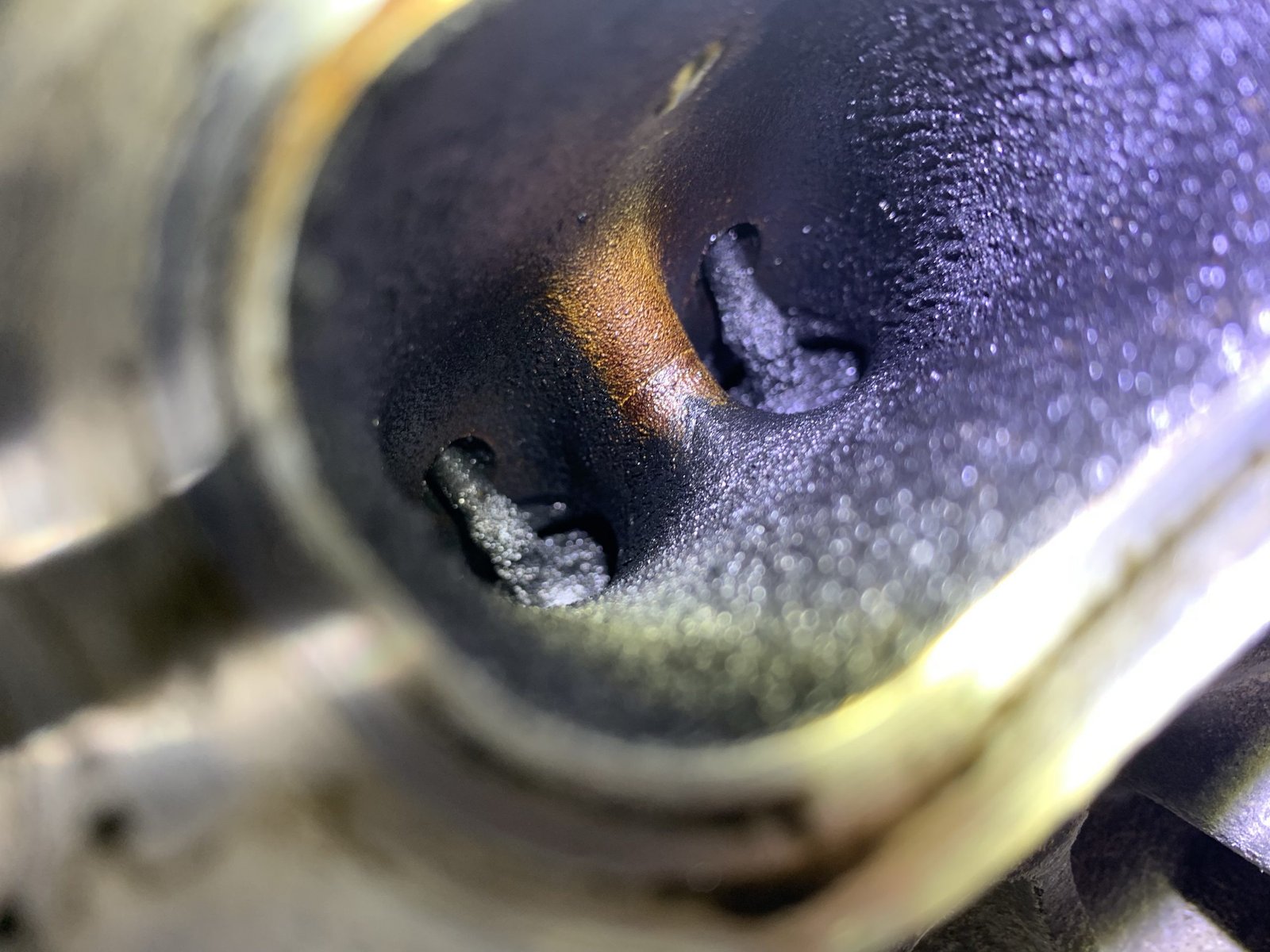
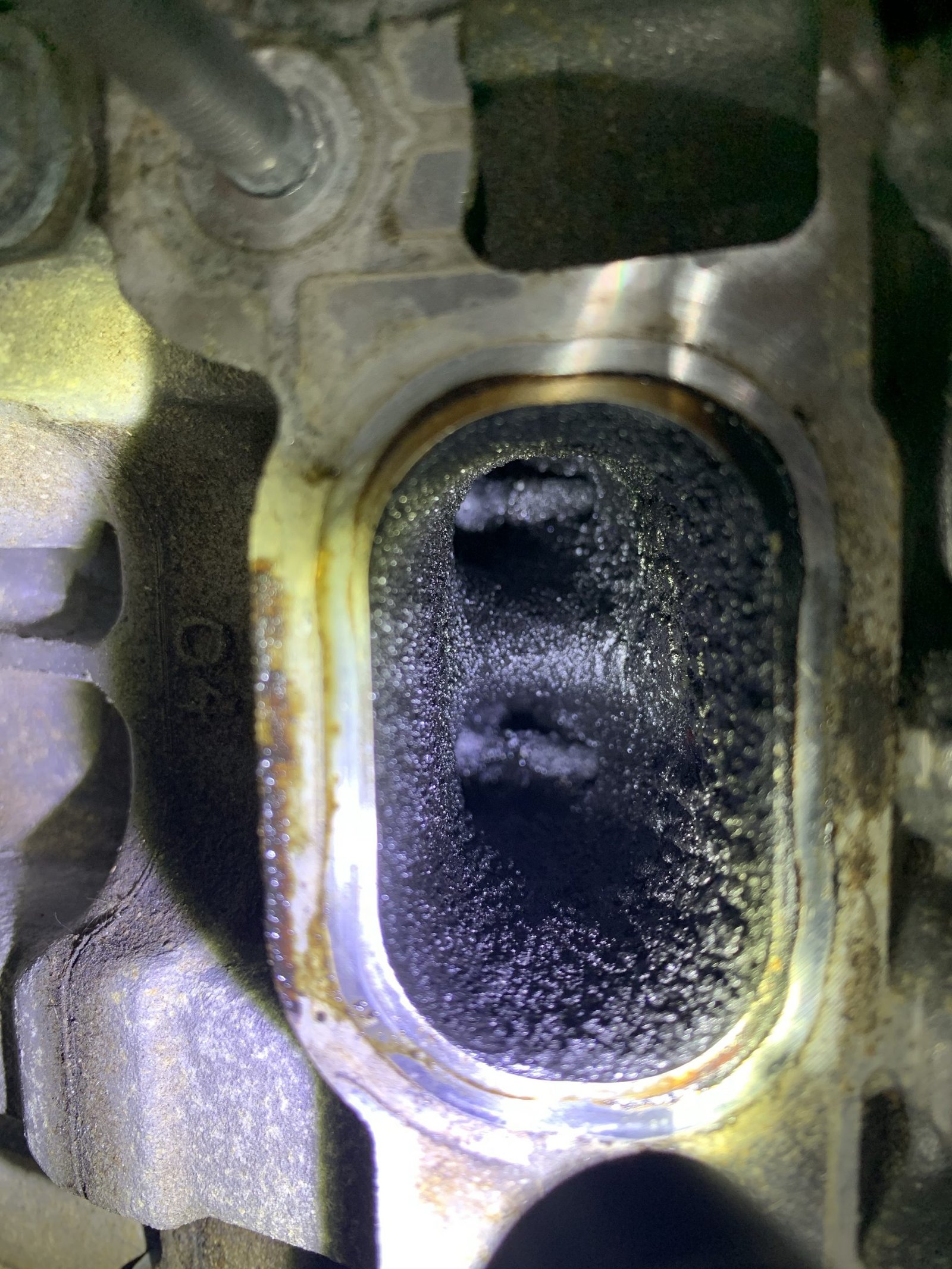
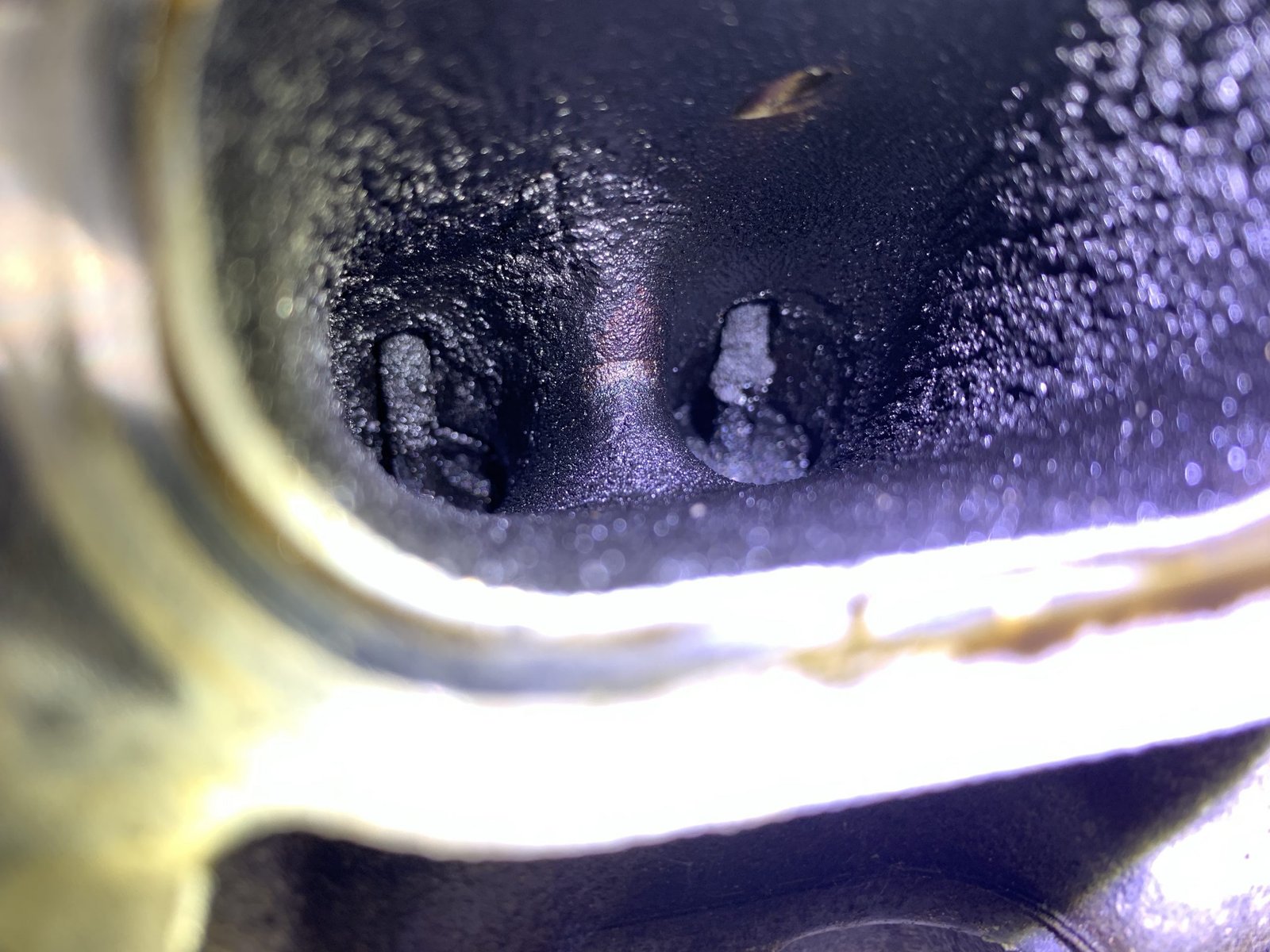
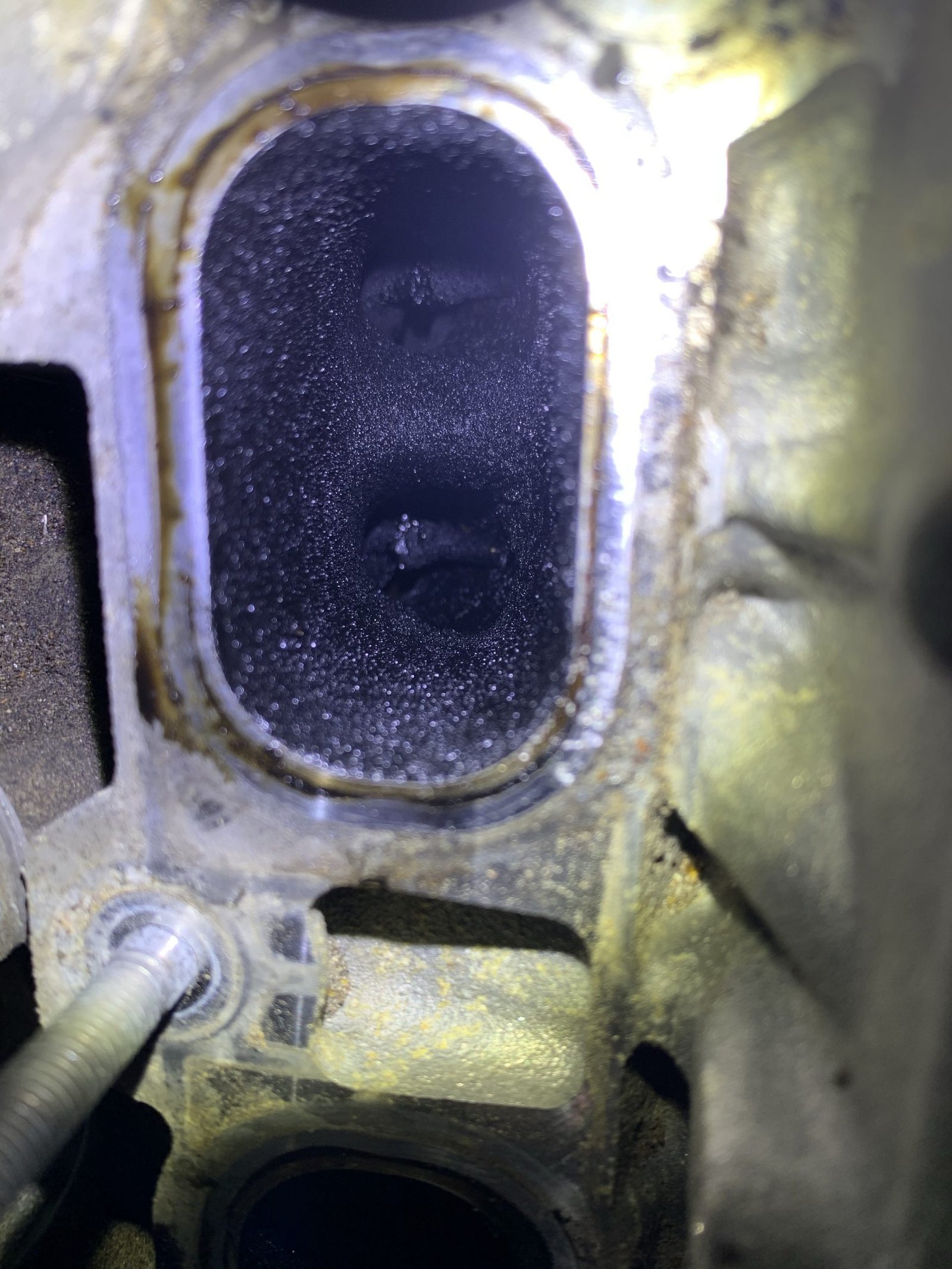
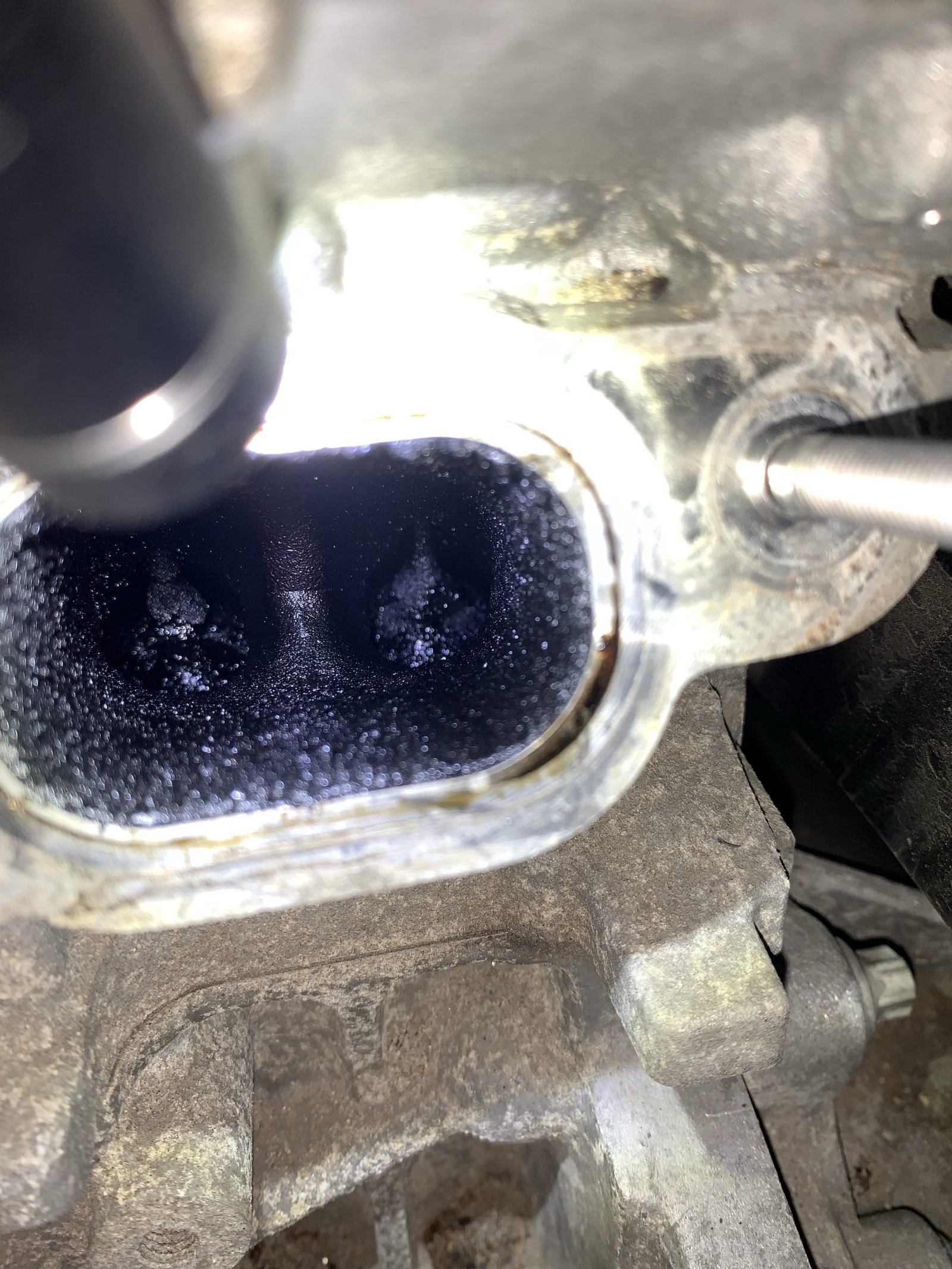
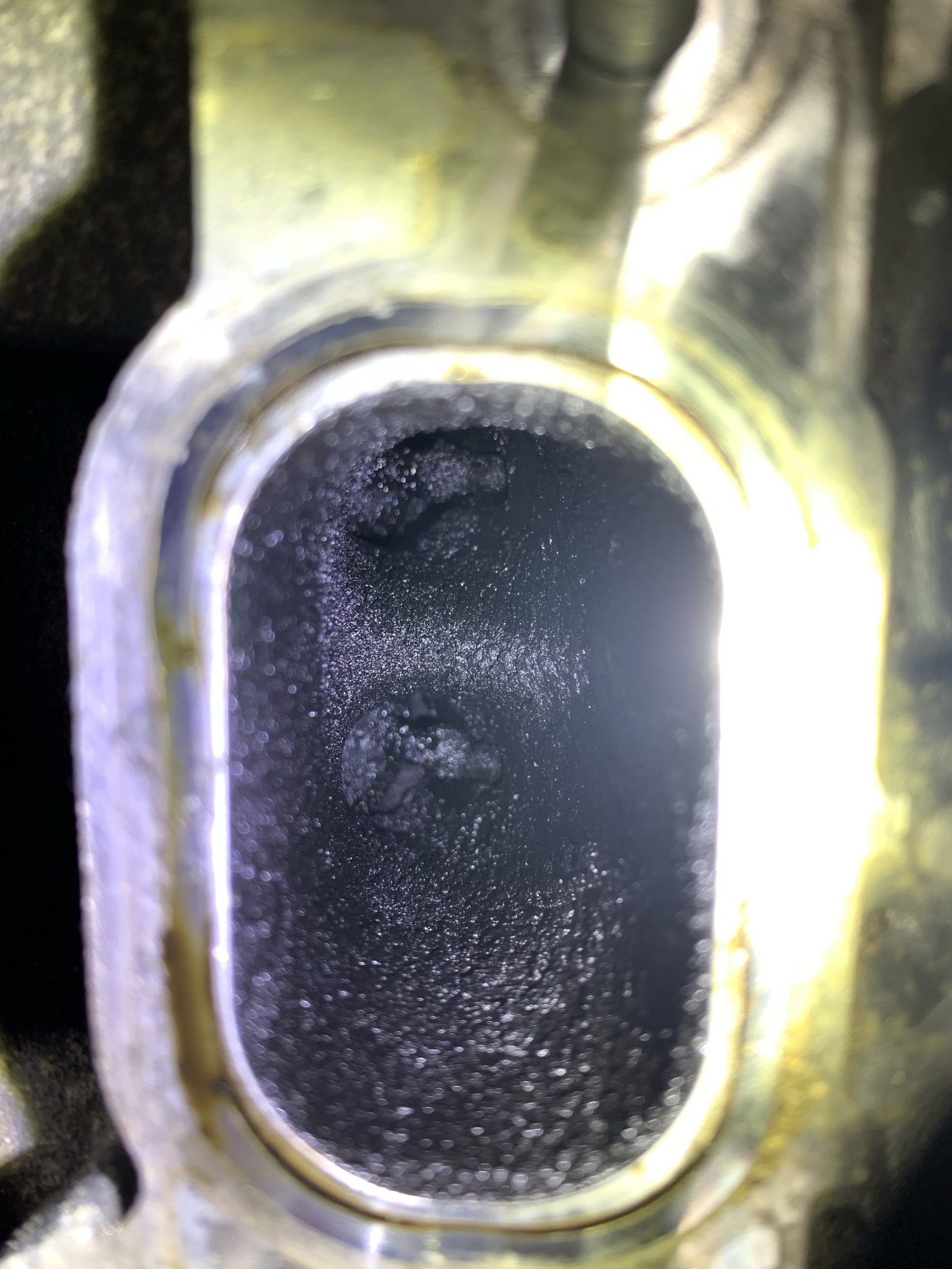
Cleaning of the intake valves can be done without major disassembly. Typically walnut shell media blasting of the valves and intake ports in the cylinder head work very well. The walnut shell media is soft enough that it won’t harm the cylinder head or valves, but does an excellent job of removing carbon. If some particles are left behind and get sucked into the engine, they will burn during combustion or get blown out the exhaust. An adapter is placed into the intake port which will be cleaned. A vacuum attaches to the adapter to suck out walnut shell media while blasting the valves. A media blaster with a wand attachment is inserted into the intake port/vacuum adapter and blasting of the carbon can be done.
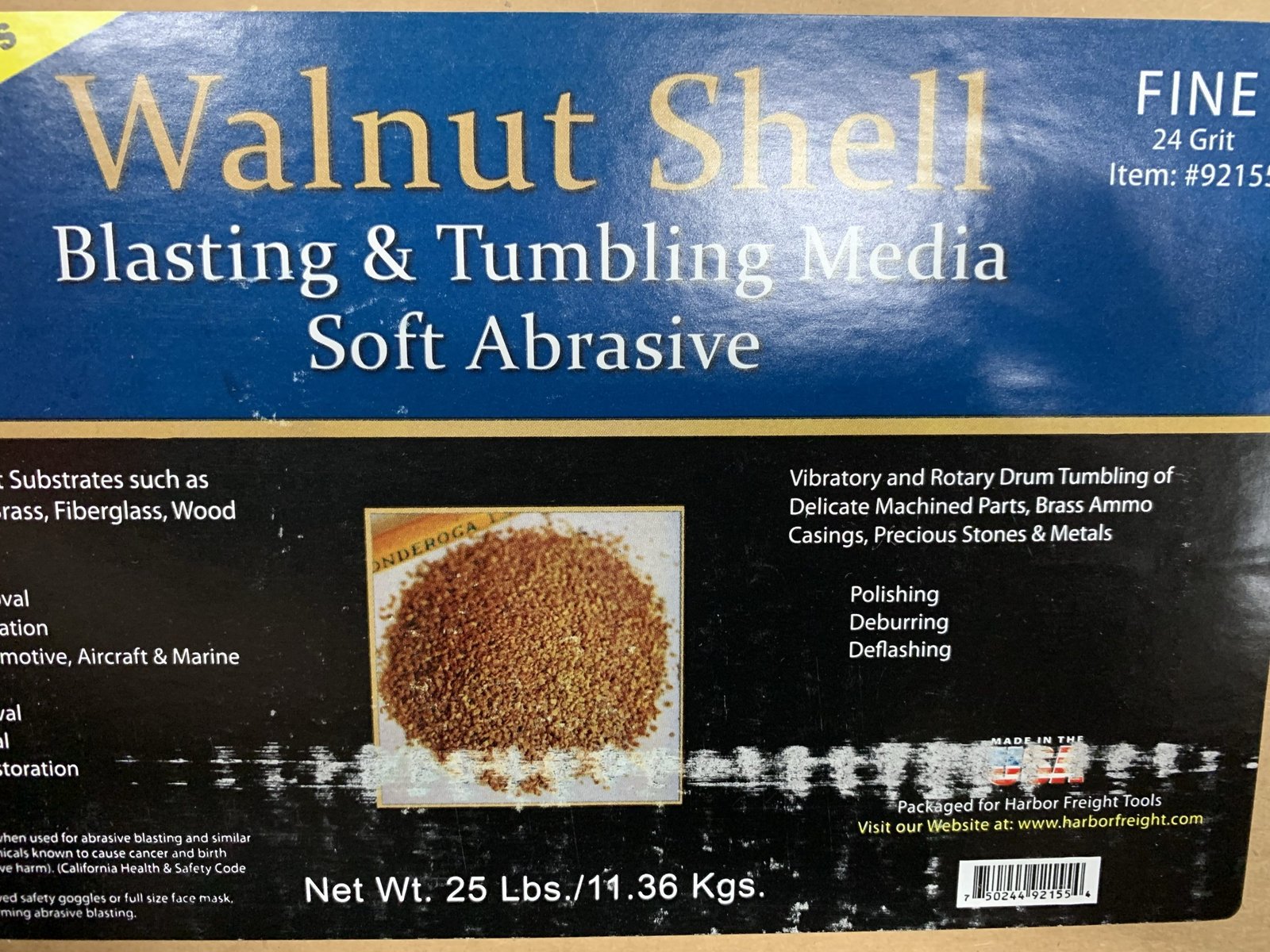
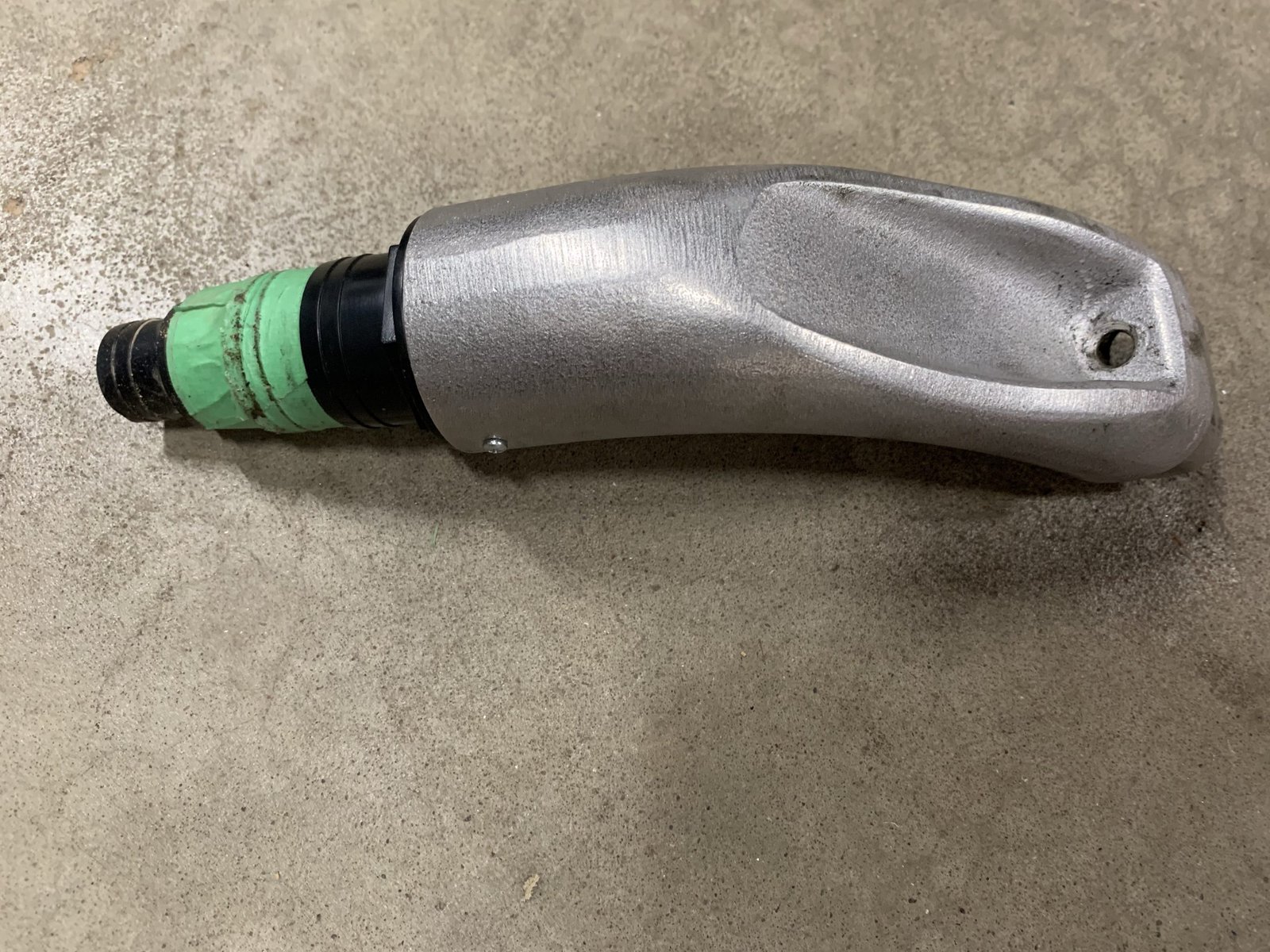
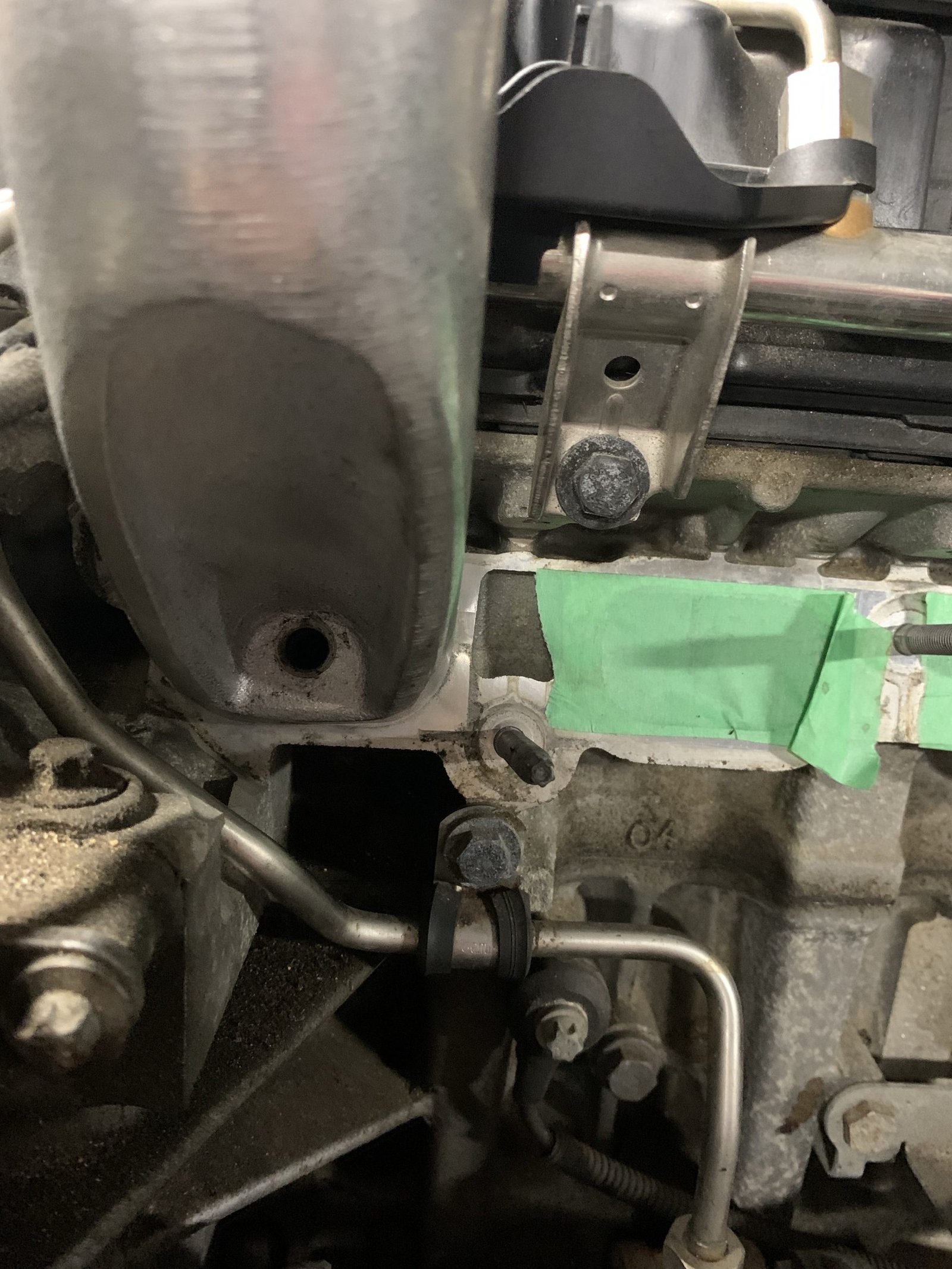
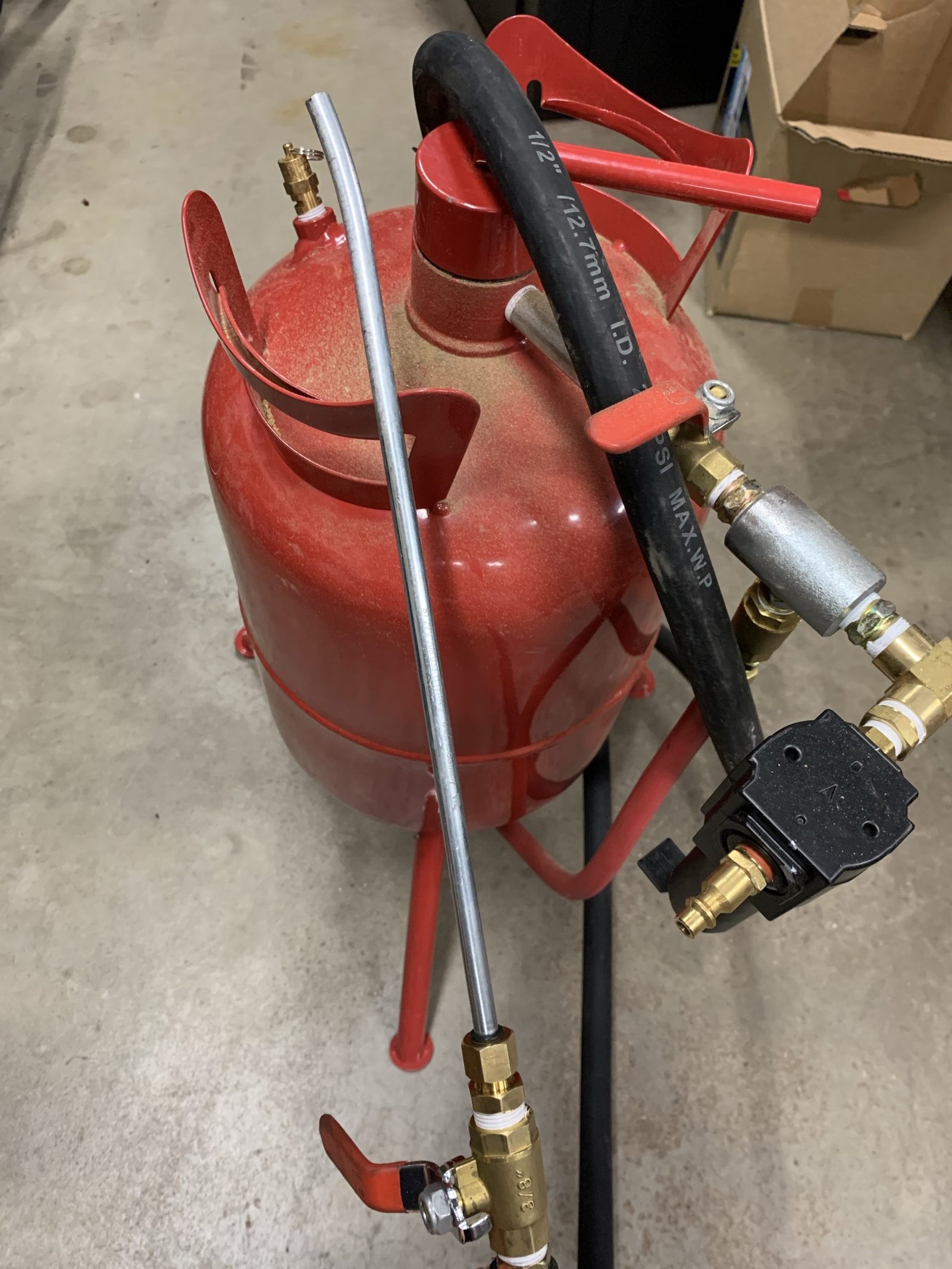
I blasted the valves and as much of the ports as possible with the walnut shells. Some areas don’t clean right away and scraping of large, deep areas of carbon will speed the process. Carburetor cleaner can also be used to soak the valves and soften the carbon. I have used a brake fluid suction device to remove the liquid and then further clean with the walnut shell blasting. It can be somewhat tedious, but the results create new looking valves and intake ports.
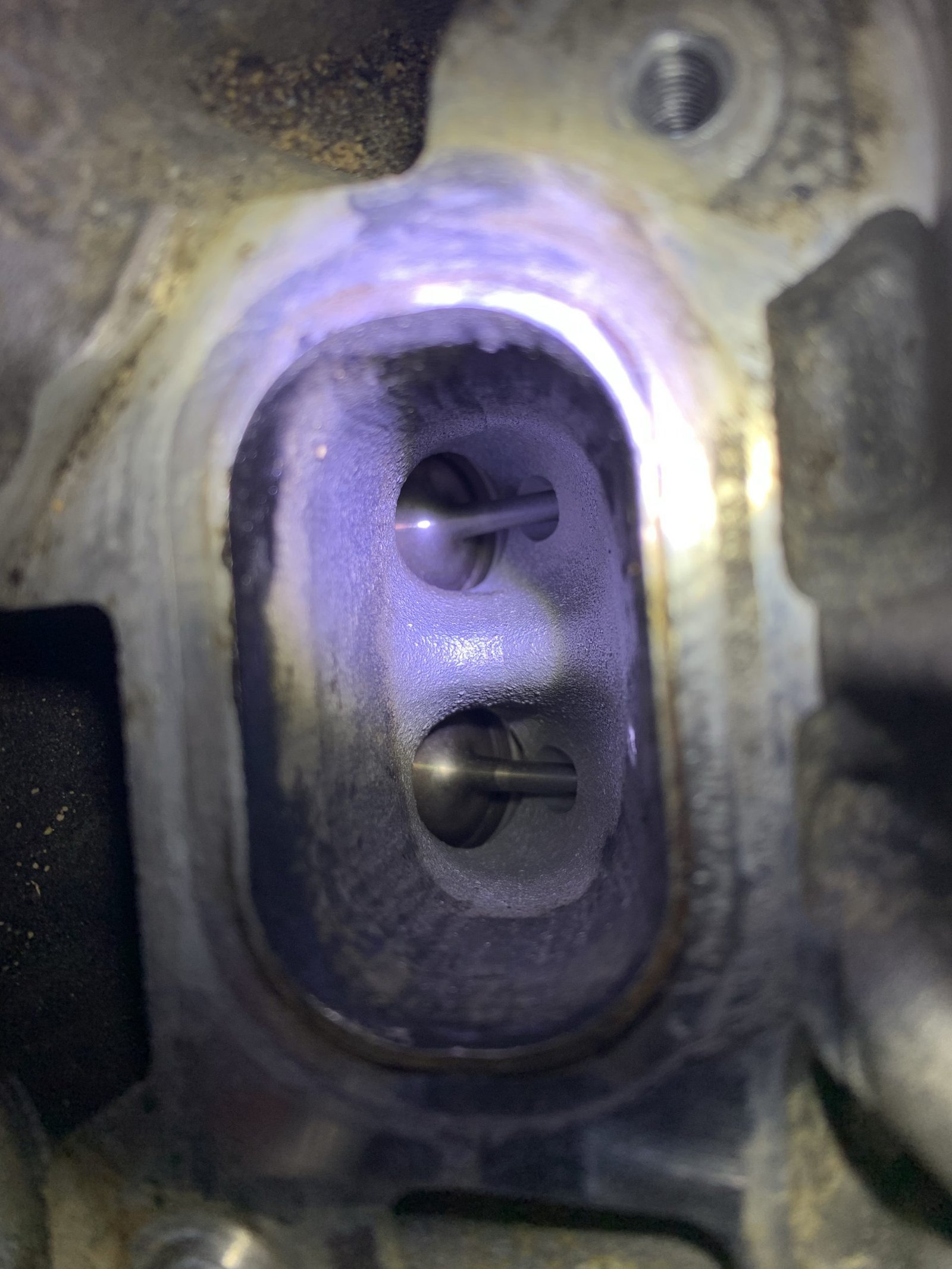
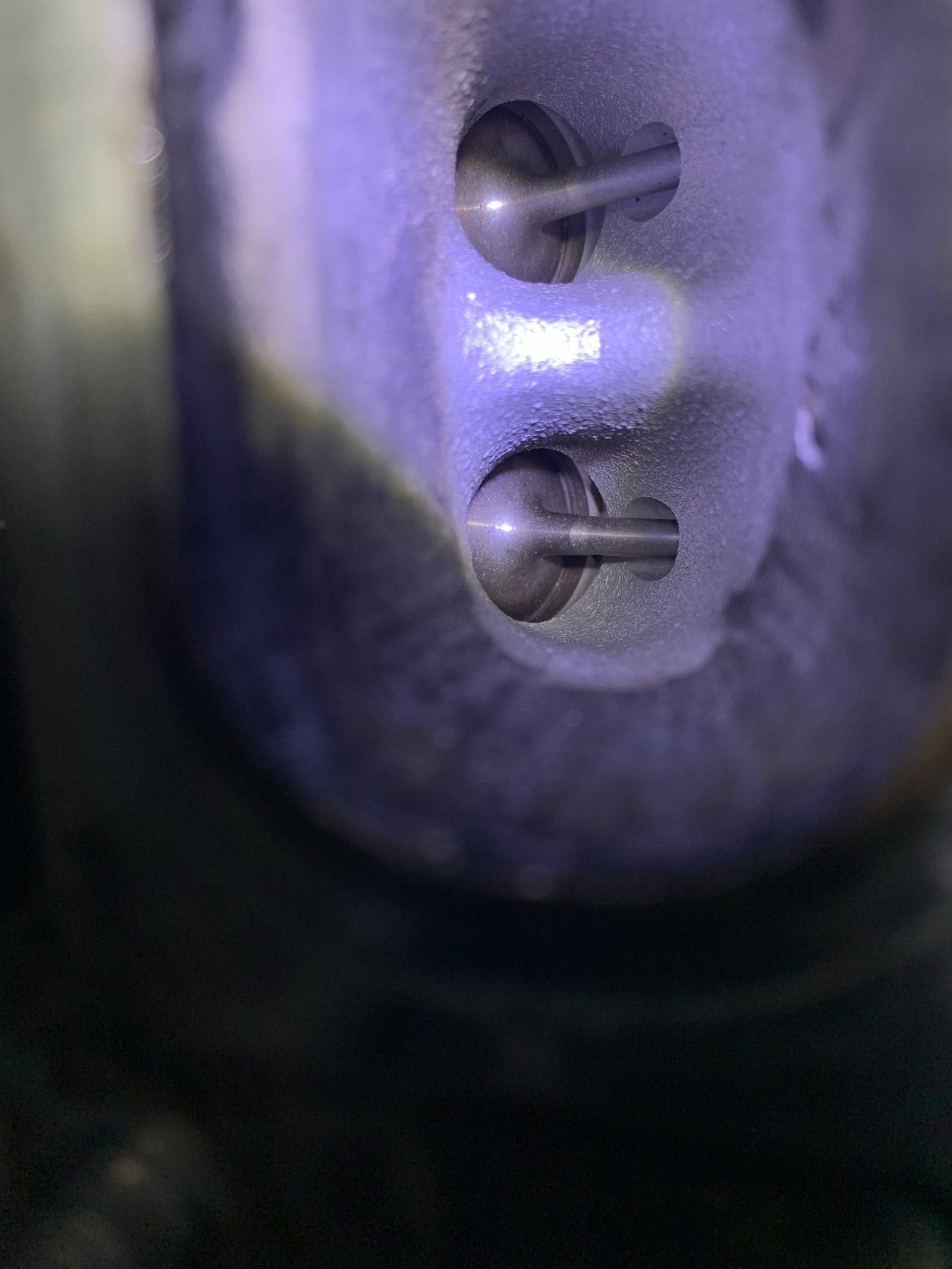